
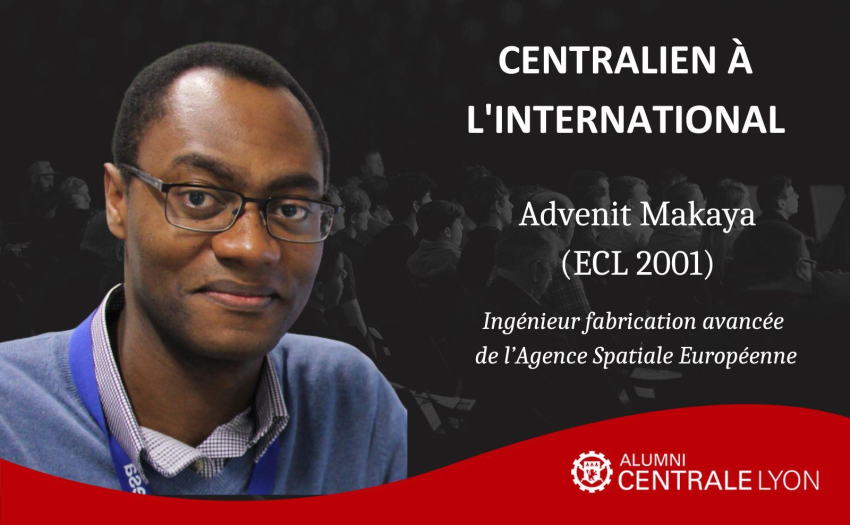
Rencontre avec Advenit Makaya (ECL2001) : Ingénieur fabrication avancée pour l’Agence Spatiale Européenne
Chaque Centralien a sa propre trajectoire. Celle d’Advenit Makaya (ECL2001) l’a propulsé jusqu’à l’Agence Spatiale Européenne où il travaille comme ingénieur fabrication avancée. Spécialiste des matériaux et procédés, ses travaux participent entre autres à la préparation des futures missions d’Exploration, telles que « Mars Sample Return », qui doit rapporter des échantillons de Mars ou « Argonaut » qui sera le premier atterrisseur Européen sur la Lune. Il revient aujourd’hui pour Technica sur son parcours et la façon dont la recherche sur les Matériaux et Procédés contribue au développement durable des activités spatiales.
Bonjour Advenit. Après votre diplôme de Centrale Lyon, vous avez enchaîné avec une thèse en traitement des matériaux. Pourquoi ce choix ? Aviez-vous déjà une idée de carrière en tête?
A mon arrivée à Centrale Lyon, j’ignorais encore dans quel domaine technologique ou pour quelles applications je voulais travailler. Aussi, la perspective de me former au sein d’une école généraliste me convenait-elle parfaitement. Au fil des cours, des stages et des projets d’École, j’ai développé deux centres d’intérêt : l’ingénierie des matériaux (comprendre de quoi sont faits les pièces et équipements utilisés dans les différents domaines d’ingénierie et comment ils fonctionnent au niveau microscopique) et l’aéronautique. Les avions et la façon dont ils fonctionnent m’ont toujours fasciné depuis l’enfance, même si je ne me rêvais ni pilote ni astronaute. Les diverses expériences en première et deuxième année à Centrale Lyon ont confirmé et renforcé cet intérêt latent.
Ayant le désir de partir à l’étranger pour ma troisième année, j’ai cherché une université qui offrait des cours dans le domaine des Matériaux. J’ai eu la chance de trouver un Master en ingénierie des Matériaux au Royal Institute of Technology, KTH, à Stockholm, en Suède. Cette formation me permettait, après un an de cours et six mois de stage, d’avoir le double diplôme de l’Ecole Centrale de Lyon et du Master of Science de KTH.
Pendant ce Master, j’ai compris que ce qui m’intéressait, ce qui me faisait vibrer, c’était d’aller en profondeur dans la compréhension de la structure et des propriétés des matériaux... plus encore que d’utiliser ces matériaux pour résoudre un problème particulier d’ingénierie. En parallèle, j’ai entretenu mon intérêt pour l’aéronautique, en choisissant un stage de fin d’études dans l’entreprise qui s’appelait alors Volvo Aero. J’y ai contribué à un projet de recherche sur le brasage des aluminures de titane, un alliage léger et résistant qui était envisagé comme alternative potentielle aux superalliages de nickel, pour les tuyères d’échappement des moteurs d’avion.
Lorsque le directeur du Master m’a proposé d’effectuer une thèse, j’ai hésité à l’idée de travailler pendant cinq ans (la durée nominale d’une thèse de doctorat en Suède) sur le même sujet. Finalement, mon fort intérêt pour aller en profondeur dans la compréhension des matériaux l’a emporté et j’ai accepté d’effectuer une thèse en traitement des matériaux (« Materials Processing » en Anglais). Mon travail consistait à développer des procédés pour produire des mousses métalliques, c’est-à-dire des matériaux métalliques très poreux, légers et résistants, pour applications potentielles dans des structures légères, que ce soit pour l’automobile ou l’aéronautique, par exemple. Même si mon travail, comme c’est généralement le cas pour un thèse de doctorat, n’a fait que poser les prémisses d’une méthode potentielle pour produire ces matériaux, loin d’une application concrète, l’expérience de la thèse a été très positive et m’a pleinement satisfaite, dans ma formation à la recherche et développement sur des matériaux innovants.
Echantillon de mousse d'aluminium
Technica : Racontez-nous votre parcours professionnel qui va passer par la Suède, le Japon, l'Angleterre puis les Pays-Bas.
Au cours de ma thèse, un résultat d’expérience inattendu m’a amené à détecter une microstructure un peu inhabituelle sur certains des échantillons de mousse d’acier que je préparais. C’était ce que l’on appelle une structure métastable, dans laquelle les atomes des différents éléments de l’alliage ne se réarrangent pas de la manière dont on l’attend, quand l’alliage métallique est solidifié rapidement. Poussé à l’extrême, c’est-à-dire quand on solidifie les alliages très vite, on obtient ce que l’on appelle une structure amorphe, dans laquelle l’alliage solide conserve l’arrangement désordonné que les atomes n’ont, en principe, qu’à l’état liquide. Cela confère toutes sortes de propriétés intéressantes au matériau métallique solide.
Après l’obtention de mon doctorat, mon directeur de thèse m’a mis en contact avec un chercheur japonais dont l’équipe faisait des travaux très intéressants sur les métaux amorphes. J’ai eu l’immense chance d’obtenir une bourse du gouvernement japonais, dédiée aux chercheurs étrangers, pour aller effectuer un postdoctorat dans ce laboratoire à Nagoya. J’ai travaillé sur le développement d’une technique pour former une structure composite dans des alliages métalliques de zirconium, avec une matrice amorphe parsemée de particules crystallines sphériques.
Microstructure d'un alliage de Zirconium avec une matrice amorphe et des particules crystallines sphériques
L’objectif était d’allier la très forte résistance des structures amorphes à la résilience des structures crystallines plus classiques. Nous avons mis au point une méthode unique pour générer ce type de structures hybrides (lien vers article issu de mes recherches à Nagoya). Bien que les propriétés n’aient pas atteint les niveaux souhaités à l’issue de mon séjour, nos travaux ont été suffisamment pertinents et originaux pour déposer et obtenir un brevet japonais, pour notre méthode de fabrication. En plus d’être très intéressant et gratifiant sur le plan professionnel, mon séjour d’un an et demi à Nagoya a été une expérience unique sur le plan humain. Vivre au Japon, découvrir un peu ce pays et m’y faire des amis a dépassé mes espérances, que ce soit en termes de découverte ou d’apprentissage.
A Kyoto en 2009
Au sortir de mon projet postdoctoral à Nagoya, j’ai postulé à la fois dans la recherche académique et en industrie. Il se trouve que c’est l’industrie qui m’a offert l’opportunité la plus concrète, sous la forme d’un emploi d’ingénieur de calcul de durée de vie (« Lifing Technologist ») chez Rolls-Royce, à Derby, en Angleterre. Je faisais partie d’une équipe qui calculait le nombre de vols prévu pour les turbines de moteurs d’avions civils, avant maintenance. Cela consistait à élaborer des modèles de simulation du comportement thermomécanique des turbines et à utiliser ces modèles pour prédire la durée de vie des turbines, sous l’effet de divers processus de dégradation, tels que la fatigue, la tolérance aux dommages etc…J’ai travaillé sur la modélisation des turbines de moteurs tels que celui des Airbus A380 ou A340. Ce travail m’éloignait un peu de l’ingénierie matériaux, mais m’a amené à compléter mon expérience en simulation mécanique. Surtout, il m’a permis de découvrir le monde industriel, beaucoup plus réactif que celui de la recherche académique et où le fruit de notre travail à des répercussions à beaucoup plus court terme sur la vie de tous les jours. J’en garde un excellent souvenir. Notamment de l’équipe internationale dans laquelle j’évoluais, faite d’un bon équilibre entre des ingénieurs expérimentés et des jeunes qui se formaient au métier.
Après quatre ans à ce poste, pour un mélange de motivations professionnelles et personnelles, je me suis mis à la recherche d’une nouvelle expérience. Cela m’a amené à postuler pour un emploi d’ingénieur Matériaux R&D à l’Agence Spatiale Européenne, où j’avais déjà postuler sans succès pour des stages. Ce poste me ramenait à ma formation première, les matériaux et aussi à des activités davantage liées à la recherche et développement. J’ai eu la chance de décrocher ce poste, en tant que contractant dans l’équipe Matériaux et Procédés, au Centre Européen de Technologie Spatiale (ESTEC), à Noordwijk, aux Pays-Bas.
Technica : En quoi consiste votre poste actuel d’ingénieur fabrication avancée à l’Agence Spatiale Européenne ?
Je fais partie de l’équipe Matériaux et Procédés dont la mission est, d’une part, de fournir un support aux grands projets (les grandes missions spatiales) de l’ESA dans le domaine des matériaux et des procédés de fabrication et d’autre part, de définir et coordonner des activités de développement de technologies pour les futurs matériaux et procédés de fabrication, qui pourraient être utiles dans les missions à venir.
Pour ce qui est du support aux projets, je contribue principalement aux missions d’Exploration, telles que « Mars Sample Return », qui doit rapporter des échantillons de Mars ou « Argonaut » qui sera le premier atterrisseur Européen sur la Lune. L’ESA agit en tant que maître d’œuvre de ces projets, c’est-à-dire que nous définissons les cahiers des charges des missions et les exigences techniques des engins spatiaux associés, nous émettons des appels d’offre à l’industrie, sélectionnons les acteurs industriels et les accompagnons dans le développement, la fabrication et les tests sur les équipements spatiaux.
Détail des trois éléments principaux d'Argonaut : l'élément de descente lunaire qui se charge de voler vers la Lune et d'atterrir sur la cible, l'élément de plate-forme de chargement qui est l'interface entre l'atterrisseur et sa charge utile, et enfin, l'élément que les concepteurs de la mission veulent envoyer sur la Lune. Copyright ESA.
En tant qu’ingénieur Matériaux et Procédés, je revois et approuve les matériaux et procédés de fabrication proposés par l’industrie, en accord avec les normes techniques européennes. J’assiste également nos partenaires industriels dans la résolution de problèmes éventuels dans le développement des équipements et je participe aux revues sur les aspects matériaux et fabrication, aux étapes clés du projet. Cela constitue une tâche conséquente pour notre équipe, étant donnée la diversité des matériaux et techniques de fabrication qui entrent dans le développement d’un engin spatial, des structures métalliques et composites, aux circuits électroniques, qui doivent tous satisfaire aux exigences de l’environnement spatial (vide, changements de températures, radiations, vibrations au lancement, entre autres...).
La deuxième partie de mon travail consiste à accompagner le développement des technologies de matériaux et procédés qui définiront la manière dont nous fabriqueront les engins spatiaux sur les missions futures. Là encore, nous proposons et sélectionnons des sujets de développements techniques, émettons des appels d’offre, revoyons les propositions reçues d’acteurs académiques ou industriels et accompagnons ces partenaires dans le développement de ces technologies. Dans ce cadre, je coordonne des activités sur une variété de matériaux et techniques de fabrications avancées, dans des domaines tels que la fabrication additive des métaux ou des céramiques, les procédés de soudure à l’état solide par friction ou encore des procédés de traitement de surface à l’impact environnemental réduit. A travers notre initiative « Advanced Manufacturing », nous recherchons et développons des technologies de fabrication qui procurent un gain significatif en matière de performance des systèmes spatiaux, de réduction de coûts ou de gains de masse, entre autres améliorations.
L’une de mes activités principales, dans ce cadre et de développer les technologies de fabrication dans l’espace, en orbite ou sur la surface de la Lune ou de Mars. La capacité de fabriquer les engins et équipements spatiaux offre, d’une part, la possibilité de s’affranchir des contraintes de taille des fusées qui devraient transporter ces équipements depuis la Terre. On peut donc construire des équipements plus grands, par exemple des panneaux solaires qui augmentent les capacités en énergie sur un satellite ou encore des antennes ou des télescopes plus grands, qui améliorent le flux de données transmis depuis la Terre ou collecté depuis l’espace. D’autre part, la possibilité de fabriquer directement dans l’espace, en particulier en utilisant les ressources trouvées sur place, permet de s’affranchir d’une partie des équipements qui seraient normalement ravitaillés depuis la Terre. Cela devient essentiel pour des missions d’exploration lointaines, telles que les futures missions sur Mars, où un ravitaillement depuis la Terre prendrait plusieurs mois. Je coordonne, par exemple le développement de démonstrateurs d’imprimantes 3D capables de fabriquer des équipements en microgravité ou encore des procédés de construction de structures de protection à base de régolithe, i.e. la poussière que l’on trouve sur la surface de la Lune ou de Mars. La fabrication dans l’espace est un domaine en plein essor, qui fait l’objet de divers programmes dans d’autres agences, au niveau international.
Technica : Cela fait maintenant 9 ans que vous travaillez à l'ESA, comment ont évolué votre poste et vos missions ? Quels sont les grands sujets d'avenir et comment pourriez-vous y contribuer ?
Je travaille depuis octobre 2014 à l’Agence Spatiale Européenne, depuis un peu plus de huit ans donc, d’abord en tant que « Materials R&D Engineer » contractant, puis, depuis 2017 en tant qu’ingénieur fabrication avancée (« Advanced Manufacturing Engineer »), directement employé par l’ESA. Avec l’expérience acquise, je coordonne un nombre croissant d’activités de développements technologiques et je contribue à former les nouvelles et nouveaux ingénieurs arrivant dans notre équipe aux différents aspects de notre activité. L’ESA a une structure hiérarchique relativement plate, avec moins de niveaux que ce que l’on pourrait trouver dans l’industrie. Cela veut aussi dire que chaque ingénieur a un volume de responsabilités important, puisque, collectivement, nous contribuons à coordonner les activités de l’ensemble de l’industrie spatiale européenne. J’ai par exemple eu à mener la définition de la feuille de route de développements technologiques dans le domaine des revêtements, pour l’ensemble des activités spatiales, en coordonnant les informations et requêtes reçues de mes collègues et des représentants des industries des 22 états membres de l’ESA, à travers leurs délégations nationales. Nous avons aussi le loisir de proposer et de développer des domaines technologiques que nous considérons utiles et prometteurs pour le spatial, comme, dans mon cas, la fabrication dans l’espace.
Parmi les grands sujets d’avenir pour l’ESA, le développement durable des activités spatiales (« Space Sustainability » en anglais) est un aspect clé. Nous devons répondre à la multiplication annoncée des capacités de lancement, par des acteurs institutionnels ou commerciaux, au défi grandissant de la réduction des débris spatiaux, ainsi que de la réduction de l’impact environnemental, sur Terre, des activités spatiales. Les Matériaux et Procédés constituent un aspect central de ces enjeux, car ils influencent le design des futurs équipements spatiaux, en particulier en termes de masse et donc d’effort de lancement, d’impact des procédés de fabrication ou encore de gestion des équipements en fin de vie. Des évolutions technologiques telles que la fabrication et l’assemblage dans l’espace peuvent contribuer à cette durabilité, en permettant la maintenance ou à l’avenir le recyclage des équipements spatiaux, limitant ainsi le nombre de lancement nécessaires au déploiement de nouveaux engins.
Technica : Du point de vue du grand public, l'Europe semble avoir pris du retard ces dernières années en matière de projets spatiaux par rapport à ses concurrents notamment américains et chinois. Qu'en est-il réellement et dans quels domaines l'Europe peut-elle et doit-elle encore être concurrentielle ?
L'Europe du spatial reste un partenaire privilégié au niveau international, comme le montre le rôle clé qu'elle a, par exemple, dans les futurs grands programmes d'exploration, tels que le programme Artemis de retour sur la Lune, où l'ESA fournit le module de propulsion et de service de la capsule Orion, ou encore la mission "Mars Sample Return" pour laquelle l'orbiteur qui ramènera les échantillons martiens sur Terre est européen. L'Europe a aussi un leadership affirmé dans certains domaines, comme l'exploration de la Terre, à travers le programme Copernicus, mené par l'Union Européenne, en partenariat avec l'ESA.
Cela dit, l'Europe a mis du temps à aborder certains tournants clés des développements spatiaux, tels que les lanceurs réutilisables ou le développement d'un secteur spatial commercial. Il y a eu une prise de conscience de ces retards et plusieurs initiatives ont été mises en place pour rattraper le temps perdu et maintenir ainsi la place prépondérante qu'a l'Europe dans le domaine spatial. On peut citer, par exemple la création du programme ScaleUp de l'ESA pour accélérer la commercialisation. Ou encore le récent rapport du groupe de conseil à haut niveau assemblé par le Directeur Général de l'ESA, qui a émis des recommandations pour augmenter l'autonomie de l'Europe dans le domaine de l'exploration.
Auteur
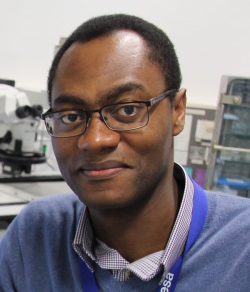
Aucun commentaire
Vous devez être connecté pour laisser un commentaire. Connectez-vous.